Program Coordinator, Technical Training
SPX Transformer Solutions, Inc. Dallas, TX, USA
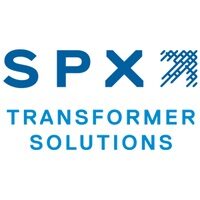
About the job
At SPX Transformer Solutions, we are committed to hiring the best and most talented people and providing them with the tools and opportunities necessary for them to not only excel at what they do every day, but also fuel their workplace passions and transform their careers. Mentoring, training and development activities by industry experts abound, while the nature of the business encourages cross-functional and interdepartmental learning, communication and teamwork that lead to continuous improvement in all areas. Desired competencies include self-motivation, creative problem-solving, compulsion to make a difference and the ability to work well with others in a challenging, fast-paced environment.
Job Summary
Functional manager with primary responsibility for the successful operation and sustainable growth of the SPX Transformer Solutions Technical Training programs. Leverage the state of the art training facilities and equipment as well as the established field based operational model to successfully achieve stated company goals for the SPX Technical Training business. Manage the day to day operations of the SPX Technical Training product line. Regularly support marketing and sales efforts to maintain a high level of customer awareness. Regularly gather competitive information and market feedback. Formulate and implement a comprehensive strategy to achieve targeted growth for the SPX Transformer Solutions Technical Training business.
Principle Duties And Responsibilities
-
- Manage allocated resources and budget to achieve stated company goals for the Technical Training Business.
- Improve market awareness and position of SPX Technical Training Business.
- Provide expert marketing and sales support to educate customers on training offerings through multiple sales channels.
- Create and manage customer specific proposals for both standard and customized engagements.
- Create, maintain, and manage Master Schedule for the Technical Training product line.
- Negotiate, enter, plan, and manage the execution of all training orders.
- For the Dallas facility, provide comprehensive event planning for training and general events.
- Manage, review, and approve all relevant training expenses to achieve stated margin and expense targets.
- Formulate and implement a regular maintenance program to ensure that the facility and training equipment is properly maintained.
- Logistical management of the fleet of Load Tap Changer training assets.
- Maintain updated training course count, content, materials, equipment, etc.
Knowledge, Skills & Abilities
-
- Excellent planning, organizational, and time management skills.
- Practical financial analysis and budget management skills.
- Advanced sales and marketing skills
- Strong presentation and negotiation skills.
- Excellent written and verbal communication skills.
- Ability to successfully engage in regular cross functional collaboration.
- Working knowledge of day-to-day business operations.
- Work efficiently under pressure.
EDUCATION AND CERTIFICATIONS
Required Education / Experience
-
- Minimum of 5 years in product/account management, business administration or similar role.
- Minimum of 2 years in a role with direct profit and loss responsibility.
- High school diploma or GED.
- Must have a valid driver’s license.
Preferred Education / Experience
-
- BS / BA degree in marketing, business administration or similar field.
- Experience with electric utilities.
Additional Information
Key Working Relationships
-
- Direct contact with training customers. Internal contact with personnel from various functional departments (Finance, Operations, Engineering, Sales/Marketing, Quality, etc.).
Physical Demands
- Ability to sit or stand for long periods of time. Ability to drive long distances in a car and/or fly in an airplane as required.
- Working Conditions
- Office environment in a batch manufacturing facility with infrequent travel to industry functions and/or customer engagements.