
Acoustic localisation of partial discharge in power transformers
Abstract Detecting partial discharges in the insulation system of a power transformer at an early stage reduces the risk of total breakdown. One method to...
byStefan Hoek, Udo Ranninger
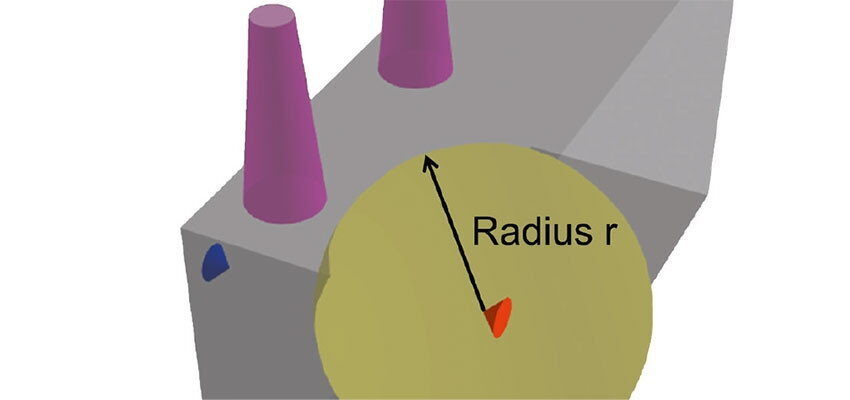
Abstract
Detecting partial discharges in the insulation system of a power transformer at an early stage reduces the risk of total breakdown. One method to detect partial discharges is acoustic measurement. With this technique detection and localisation of partial discharge is possible by placing acoustic sensors on the surface of the transformer tank. The low impact of electrical interferences from outside the measurement set-up constitutes one of the strengths of the acoustic method. A further advantage is the ability to identify the position of the partial discharge source, which is needed to estimate the risk and to enable a fast and effective repair. The sensitivity and accuracy of the PD localisation can be improved with a combination with conventional electrical measurement or with Ultra High Frequency (UHF) measurement method. Since the UHF measurement method is more advantageous for measurement environments with heavy interferences in the field, the combination with acoustic localisation proves to be useful even in challenging field situations. This article describes the application of this procedure illustrating it with different practical examples.
Keywords: power transformer, partial discharge, acoustic localisation, electrical trigger, UHF range
Introduction
The localisation of Partial Discharge (PD) faults in transformers is often necessary when such incipient faults are identified. The measurement of partial discharge level in accordance with IEC 60270 is a procedure established throughout the world for quality assurance of transformers and is performed as part of the today routine measurements at the manufacturer’s factory. If the occurrence of PD in the transformer has been determined during such a measurement, it is a matter of urgency to localize the fault, which is often very small, as quickly and accurately as possible. Similar applies to transformers in the field. Here, PD detection and localisation procedures are generally initiated as a result of corresponding indications obtained from the Dissolved Gas-in-oil Analysis (DGA) as well as from PD monitoring. A precise localisation can help to optimize the production of power transformer or can help by an effective maintenance during operation.
An established procedure for localisation of PD faults in transformers involves acoustic localisation of the PD signals using several piezoelectric sensors that are attached to the outside of the tank wall. A combination with conventional electrical measurement or with UHF measurement method can improve the sensitivity and the accuracy of the PD localisation. Since the Ultra High Frequency (UHF) measurement method is more advantageous for measurement environments with heavy interferences in the field, the combination with acoustic localisation proves to be useful even in challenging field situations. The application of this procedure is described in this article, also using different practical examples.