
Vibration-measurement-based condition monitoring
A transformer's winding modal characteristics (e.g., natural frequencies, mode shapes) are largely determined by its structural stiffness and mass distribution.
byFan Zhang et al.
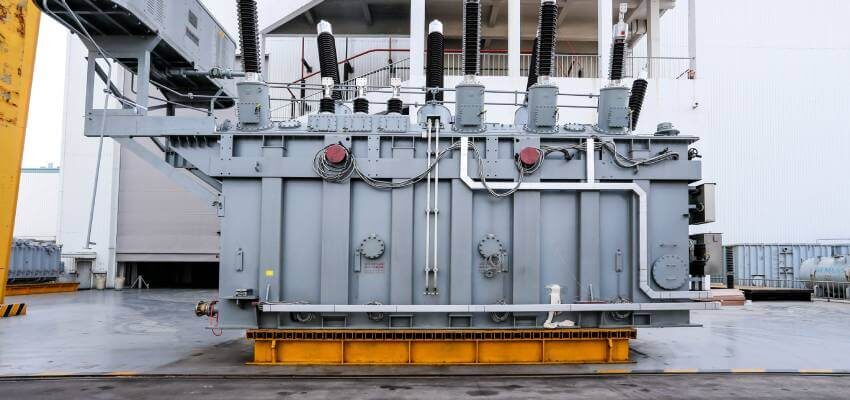
- Introduction
Transformer vibrations mainly come from the core and windings. Previously, vibrations of the iron core were identified as the main source. With the improvement of design and manufacture, especially the use of Hi-B silicon steel sheet, the adoption of step-lap cores, and the reduction of the flux density, the cores’ vibration has been reduced significantly, and windings’ vibration caused by load current becomes a considerable contributor [1]. With time, the size of transformers has increased significantly both in capacity and voltage, resulting in an increase in the vibration of large power transformers. Besides the capacity, vibrations are determined by silicon steel materials, structure design, and magnetic flux density. Therefore, a comprehensive understanding of the vibration generation and transmission in power transformers is necessary.
A transformer’s winding modal characteristics (e.g., natural frequencies, mode shapes) are largely determined by its structural stiffness and mass distribution. Changes in the transformer’s winding condition can be reflected from the changes in all or a subset of its oscillatory modes. Most of the previous analyses have focused on discrete frequencies (e.g., multiples of power frequency) of the measured vibration signals for assessing the winding mechanical condition. Hong Zhou proposed a winding vibration with the electromagnetic force analysis to obtain the steady-state vibration distribution of the axial direction [2]. Kaixing Hong used the principal component analysis (PCA) to extract vibration features from multi-sensor vibration signals [3]. He also put forward a classification model based on the support vector machine (SVM) to identify the mechanical condition of the windings [4, 5]. Bartoletti used the total harmonic distortion (THD) to identify the health condition of the transformer winding [6]. Bagheri proposed a regression model and a diagnostic criterion based on THD to monitor the inter-turn fault with the Internet of Things (IoT) technology and cloud computing, respectively [7, 8].
Other than the diagnosis based on discrete frequencies, Shao et al. introduced a method to acquire the FRFs under the currents with different frequencies [9]. Wang et al. proposed a similar method [10]. These two methods required a current or a voltage amplifier to generate a frequency-variant excitation. Instead of using the frequency-variant excitations, several researchers have analysed transient vibration signals [11, 12]. S. Banaszak and E. Kornatowski analysed the dependency describing the changes of the normalised power spectral density (PSD) to distinguish the core and the windings conditions in the steady-state and the transient energising process [13, 14].
In the past decade, researchers in Xi’an Jiaotong University and The University of Queensland have been working together to investigate the vibration characteristics of power transformers and develop vibration measurement-based condition monitoring of transformer windings. Their work focuses on three main aspects (1) investigating the sources and significances of different type excitation; (2) extracting and analysing modal characteristics from measured vibration signals; and (3) inferring the changes in winding mechanical condition. This article presents key findings in these three aspects.
Log in or subscribe to read the whole article.