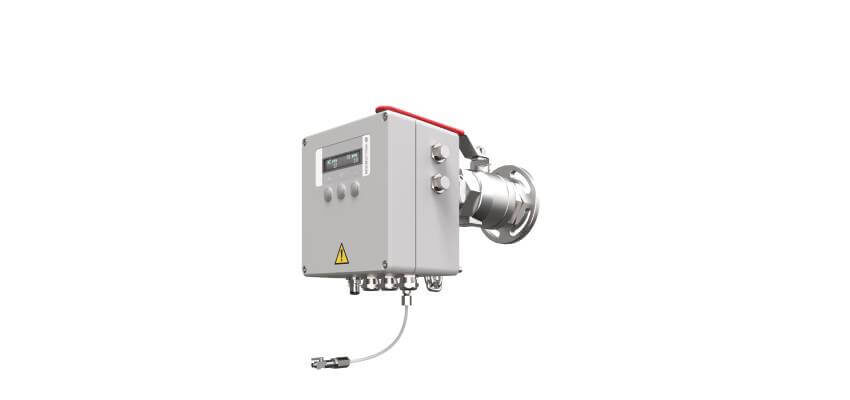
Why should DGA monitoring be stable under vacuum pressure?
Germany, Regensburg: MR presents its MSENSE® DGA 2/3 online analysis device.
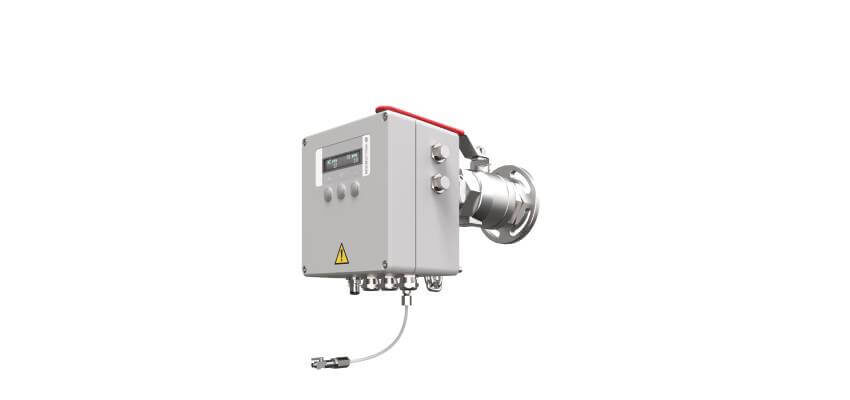
Image source: MR
Germany, Regensburg: MR presents its MSENSE® DGA 2/3 online analysis device.
During the production process and when filling power transformers with insulating liquid, the resistance of components and modules to vacuum pressure is an important aspect.
Maschinenfabrik Reinhausen GmbH (MR) also demanded this of the MSENSE® DGA 2/3 product and confirmed the results in a type test.
The MSENSE® DGA 2/3 online analysis device was tested at 5 Pa (0.05 mbar abs.) over 48 hours.
Vacuum resistance was confirmed by a subsequent test at 100 % functionality.
A customer benefit of the device is that reinstallation or shutting off during the vacuum drying process or during filling is not necessary. Leakages, malfunctions in the process or additional expenses are thus avoided, subsequent operation is ensured, and costs are saved.
The advantages of vacuum resistance are obvious: operating safety and cost savings.
The main focus of DGA monitoring should be reliable condition diagnostics.
According to experts and international standards, hydrogen, carbon monoxide and moisture in the insulating oil of power transformers are the primary early indicators of potential thermal or electrical damage to the transformer (IEC 60475, IEC 60567, ASTM D 4057).
MSENSE® DGA 2/3 offers a crucial benefit for operational safety based on continuous monitoring of these early indicators for identifying thermal and electrical faults in oil-filled, paper-insulated power transformers.
Additional trend detection, combined with recommended courses of action, allows the lifetime of the equipment to be significantly extended.
If you would like more information about MR’s products and services, visit the company’s homepage www.reinhausen.com.
Source: MR
#DGA monitoring#Germany#Maschinenfabrik Reinhausen GmbH (MR)#MSENSE® DGA 2/3#oil-filled power transformers